For a few days in mid February, a workbench inside the radiofrequency (RF) laboratory at NYU Langone Health became a de facto manufacturing and order-fulfillment station as engineers assembled the first outbound specimen of the latest hardware resource offered by the Center for Advanced Imaging Innovation and Research: a benchtop RF coil interface compatible with a new Siemens standard called Tim 4G.
The Tim 4G technology, proprietary to Siemens, reduces the number of cables needed for RF coil arrays to sync with an MRI scanner by allowing a single connector to serve up to 24 coil channels—triple the number supported by the company’s previous system.
“The upgrade also made the testing equipment different,” said Bili Wang, research engineer at NYU Langone who led the development of the benchtop interface. Wang joined the research team in 2018 and soon afterward began working on a 24-channel flexible glove coil, a project led by Bei Zhang, PhD, and Martijn Cloos, PhD, who were with NYU Langone at the time. For convenience, the engineers decided to use a Tim 4G connector as doing so meant that there would be just one cabled connection to the scanner, simplifying the experience for MRI technologists and patients.
However, the engineers did not have a benchtop interface compatible with such a system and had to “manually daisy-chain the power supply in order to go to all the different channels,” Wang said, which was “doable” but “very tedious.” So, she built a prototype interface that made development easier.
“My first design was like a mumbo jumbo of cables,” Wang said. But the instrument worked so well that she quickly improved on it with a second, better organized version. Along the way the team realized that its need likely reflected similar demand at other research groups that develop custom RF coils for advanced MRI applications, and “we decided to make a [third] version that is more shareable, more manufacturable.”
Benchtop interfaces simulate the signals exchanged between the coil array and the MRI system, allowing engineers to test coil designs and the behavior of the sensitive electronics involved. The instruments are critical to RF coil development because most of the work cannot be performed at the actual MRI machine.
“It’s not as easy as you think to use an MRI scanner as a troubleshooting device,” said Ryan Brown, PhD, associate professor of radiology at NYU Langone and scientist at the Center for Advanced Imaging Innovation and Research. He explained that a cylindrical bore inside a strong, always-on magnet controlled by complex software is an impracticable environment for debugging coil circuitry. By comparison, a benchtop coil interface emulates the relevant signals while sparing engineers the multivariate complexity that comes with a whole MRI system.
For the RF team developing the 24-channel flexible glove coil, the payoff of working with an interface was immediate. “It’s already played a vital role in freeing up design bottle necks in our lab,” said Dr. Bown. “We knew it would be valuable for others in the community.”
But building a one-off for own use is not the same as building a resource for others and “can cause headaches in terms of what parts are available and functional,” Dr. Brown said. “It’s a really painstaking effort to find the exact component that will do the job in concert with the rest of the device.”
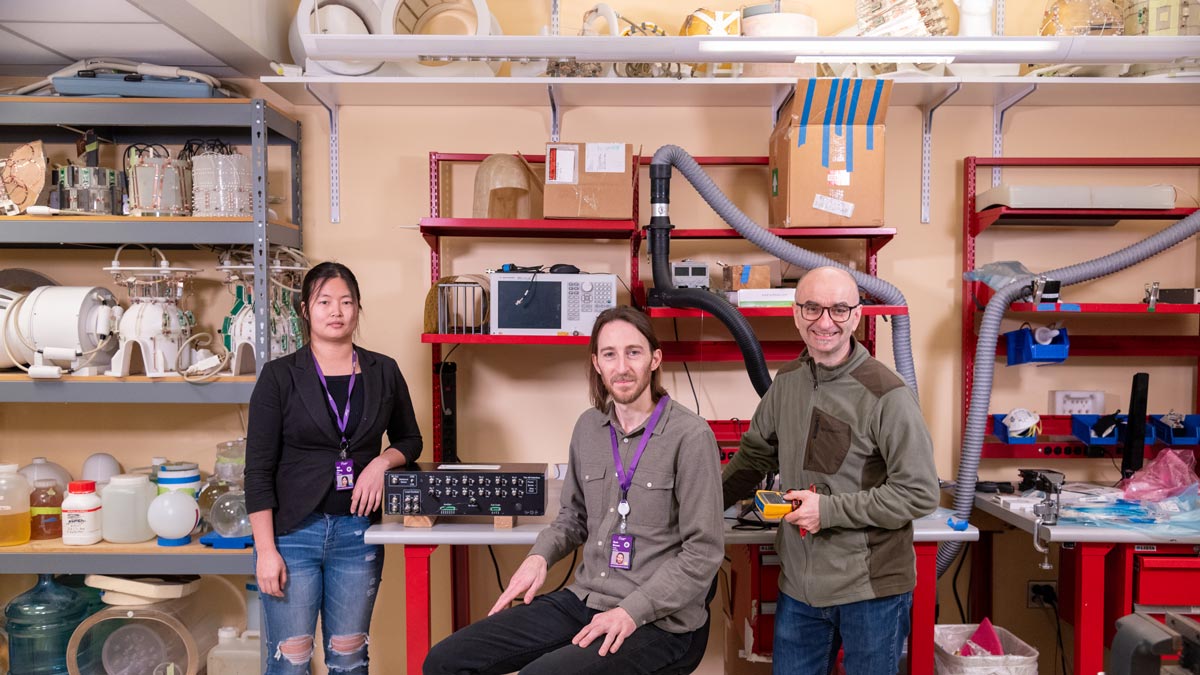
To make sharing the benchtop interface viable, the team redesigned the handmade components as printed circuit boards (PCBs) that could be made to order by a PCB house. Rather than copying the interface, team members reengineered it again with an eye to facilitating its shareability and minimizing the amount of labor needed onsite to finalize each unit.
“It’s pretty intricate,” said Douglas Brantner, MS, research engineer at NYU Langone and the Center for Advanced Imaging Innovation and Research who led the PCB design. A lot of thought went into connection management and power handling because the interface involves multiple voltages, he said. Outsourcing the board production allows the team to have most of the electrical components attached to the PCB at the factory via surface-mount technology. “It eliminates like 90 percent of hand soldering,” Brantner said.
Although miniaturization and small-batch manufacturing have made the provision of such specialized resources possible, assembly still requires labor. It takes the engineers a few days to install all the parts, solder the remaining components, and test the device. The team considered sharing documentation instead of offering a working instrument but determined that doing so wouldn’t be as helpful. Instead, the benchtops are available upon request, at cost.
“Scanner architecture continues to become more complicated, and benchtop interfaces—like the one we built—have to be designed to replicate certain features of the scanner,” said Dr. Brown.
The first unit was shipped to Polytechnique Montréal, where it will facilitate research and development on RF coils for advanced applications in neuroimaging. RF engineering teams at other research institutions that build novel MRI hardware are welcome to inquire, Dr. Brown said. “If they’re building an array that has a high number of channels, it’s indispensable.”
Visual Story
Related Resource
An electronic interface for research and development on radio frequency coils built for Siemens Healthineers Tim 4G.
Related Story
Imaging scientists around the world are looking into this simple transmitter to deal with breathing motion in MRI scans. NYU Langone offers resources to kickstart their research.